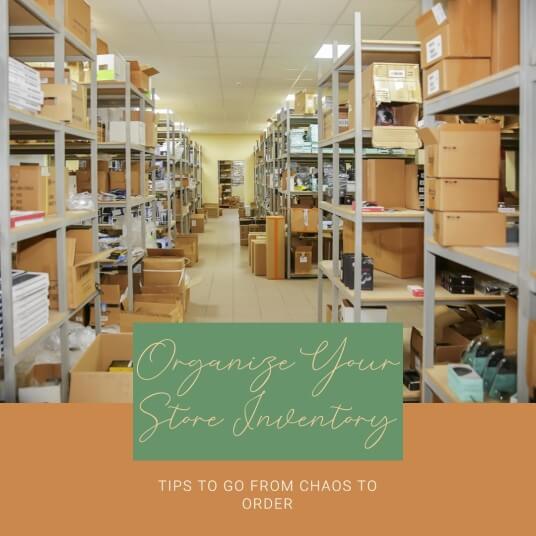
In the bustling realm of retail, maintaining a well-organized store inventory is vital for efficient operations and exceptional customer service. Yet, achieving order amidst the chaos of daily transactions and merchandise movement can seem like a daunting task. Fear not! With the right strategies and tools, you can transform your store inventory from chaos to order. Let’s explore some essential tips, including how POS systems and POS suppliers can play a pivotal role in this process.
1. Conduct Regular Audits:
Regular inventory audits are fundamental for effective organization. Schedule periodic audits to assess stock levels, identify discrepancies, and address any issues promptly. Utilize your POS system’s inventory management features to streamline the audit process and maintain accurate records.
2. Categorize and Label Inventory:
Segment your inventory into categories based on product type, size, color, or any other relevant criteria. Use clear and consistent labeling to make it easy for staff to locate items quickly. Your POS system can facilitate this by allowing you to assign specific categories and tags to each product.
3. Implement a FIFO System:
Implementing a First-In, First-Out (FIFO) system ensures that older inventory is sold before newer stock. This practice minimizes the risk of spoilage or obsolescence and helps maintain freshness and product quality. Your POS system can track product expiration dates and automatically prioritize older stock during sales transactions.
4. Optimize Storage Space:
Maximize available storage space by utilizing shelves, racks, bins, and other organizational tools effectively. Arrange products logically and accessibly, with frequently sold items placed within easy reach. Your POS supplier may offer recommendations for compatible hardware or storage solutions to optimize space utilization.
5. Utilize Barcode Scanning:
Invest in barcode scanning technology to streamline inventory management processes. Barcode scanners integrated with your POS system enable fast and accurate tracking of incoming and outgoing stock, reducing errors and improving efficiency. Collaborate with your POS supplier to ensure seamless integration and optimal scanner functionality.
6. Set Reorder Points:
Determine minimum and maximum inventory levels for each product and set reorder points accordingly. Your POS system can generate automated alerts when stock levels fall below a predetermined threshold, prompting timely reordering to prevent stockouts. Work with your POS supplier to customize reorder settings to align with your business needs.
7. Train Staff Effectively:
Provide comprehensive training to your staff on proper inventory management procedures and the use of POS system features related to inventory control. Empower them to accurately record transactions, update stock levels, and troubleshoot any issues that arise. Your POS supplier may offer training resources or support services to assist in staff education.
8. Monitor Sales Trends:
Utilize your POS system’s reporting capabilities to analyze sales trends and forecast demand for specific products. This insight enables informed purchasing decisions, ensuring that you maintain optimal inventory levels without overstocking or understocking. Collaborate with your POS supplier to customize reporting tools and dashboards to track key performance indicators relevant to your inventory management goals.
Conclusion:
By implementing these tips and leveraging the capabilities of your POS system and POS supplier, you can transform your store inventory management from chaos to order. With efficient organization and accurate tracking, you’ll improve operational efficiency, enhance customer satisfaction, and ultimately drive success in your retail business.