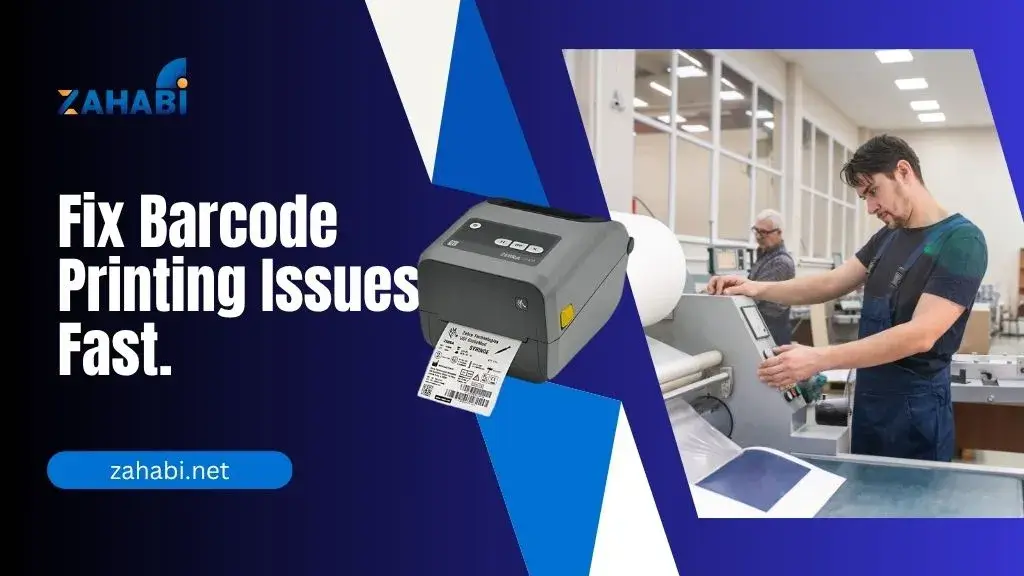
In the retail, manufacturing, healthcare, and logistics environments, barcodes are essential tools for efficient inventory management, product tracking, and data accuracy. However, businesses often encounter several recurring issues with barcode printing—ranging from poor print quality to hardware compatibility. Understanding these challenges and knowing how to address them with the right solutions can drastically improve operations and reduce costly errors.
Here’s a look at the most common barcode printing challenges and the solutions that can help overcome them.
1. Poor Print Quality and Scanning Errors
Challenge:
Faded, smudged, or distorted barcodes often result in scanning failures. This can lead to delays in order processing, inventory errors, and frustration at checkout or in warehouses.
Solution:
Invest in high-resolution barcode printers with thermal transfer printing for durable, crisp labels. Regularly maintain printheads and use quality label stock and ribbons to prevent ink bleed or fading. Also, configure printer settings according to label size and material for optimal output.
2. Label Mismatch and Incorrect Barcode Data
Challenge:
Human error during label creation or printing can result in incorrect product labeling, leading to tracking issues, misplaced shipments, and customer dissatisfaction.
Solution:
Use barcode design software that integrates directly with inventory databases or ERP systems. This allows for real-time data pulling and minimizes manual entry. Implement data validation features and use templates to standardize label formats across departments or locations.
3. Printer Downtime and Maintenance Delays
Challenge:
Frequent printer breakdowns or long maintenance times reduce productivity, especially during peak business hours or seasonal demand.
Solution:
Choose industrial-grade barcode printers with a proven track record for durability and reliability. Opt for models that offer user-replaceable parts like printheads and rollers. Schedule regular preventive maintenance and keep backup supplies and spare components on hand to avoid disruptions.
4. Incompatibility with Other Systems
Challenge:
Barcode printers that don’t integrate well with warehouse management systems (WMS), point-of-sale (POS), or mobile devices can create data silos and inefficiencies.
Solution:
Adopt printers with flexible connectivity options—USB, Ethernet, Bluetooth, and Wi-Fi—and compatibility with major operating systems and software platforms. Cloud-based barcode printing solutions also enable remote access and centralized control across facilities.
5. Label Adhesion Issues
Challenge:
Labels that peel off, fade due to exposure, or don’t stick well on specific surfaces create tracking issues and rework costs.
Solution:
Use label materials tailored to the application environment—weatherproof, heat-resistant, or tamper-evident labels for specialized needs. Conduct surface tests before mass printing and work with vendors who offer a range of material options.
6. Scalability Constraints
Challenge:
As businesses grow, managing a higher volume and diversity of products requires scalable barcode printing without sacrificing consistency or speed.
Solution:
Implement centralised label management systems and networked printers. These allow consistent printing templates and batch processing across multiple locations. Cloud integration further supports scalability with minimal hardware changes.
Read this blog to discover how barcode printers enhance modern business efficiency.
Final Thoughts
Barcode printing is not just a back-office function’s a critical link in ensuring accuracy, efficiency, and customer satisfaction across supply chains. By proactively identifying pain points and adopting the right combination of hardware, software, and maintenance strategies, businesses can tackle frequent barcode printing challenges head-on.
Whether you’re a warehouse manager, IT lead, or retail operator, investing in reliable barcode printers today can future-proof your operations and unlock new levels of performance and traceability.